Pipeline-monitoring UAV research takes off at ACE Climatic Wind Tunnel
April 9, 2018
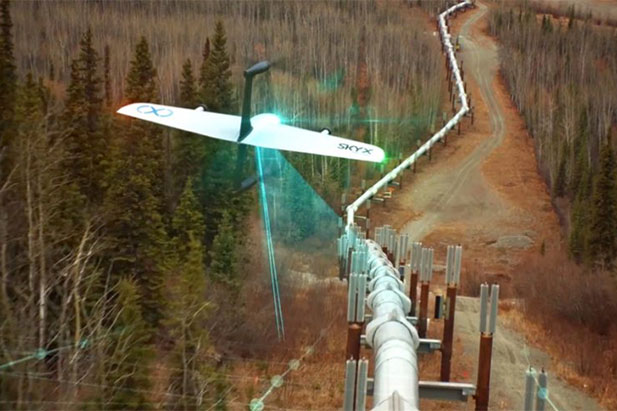
Across North America, nearly four-million kilometres of pipe (for oil and natural gas) crisscrosses the continent, most of it in remote locations. Industry spends almost C$50 million annually to inspect these pipelines. Aircraft, pilots, fuel, ground inspectors and satellite imagery contribute to the high cost.
One solution to save time and money is to use drones, or as the industry calls them, ‘unmanned aerial vehicles’ (UAVs). Equipped with cameras, UAVs operate with a ground-based controller and a sophisticated communication system on the aircraft.
Canadian company SkyX builds vertical take-off and landing (VTOL) UAVs that can be dispatched anywhere, anytime, easily and quickly—and in most weather conditions.
To ensure the company’s SkyOne UAV meets and exceeds safety regulations and operates as efficiently as possible, SkyX turned to the powerful research and development capacity of the University of Ontario Institute of Technology’s ACE Climatic Wind Tunnel. ACE’s massive testing chambers, including the Climatic Wind Tunnel and Multi-Axis Shaker Table (MAST), provided the ultimate controlled environment for examining SkyOne’s performance in a wide range of conditions. This type of testing would take months if completed in the field. ACE compressed the testing timeframe to just one week.
How the SkyOne UAV works
SkyX’s VTOL technology uses a quadcopter system at takeoff and then switches to a faster and more efficient fixed-wing system once the UAV reaches an appropriate altitude. The UAV pairs with SkyX’s ‘Sky Centre’ (mission control), where SkyX remotely programs and initiates autonomous flights.
To enable SkyOne for long-range flights, charging stations are placed strategically along pipelines where UAVs can land, download data and recharge without needing to return to a distant ‘home’ base. The system’s versatility makes pipeline inspections in hard-to-reach regions safer, faster and less expensive.
MAST testing process at ACE
The MAST simulates vibrations and turbulence SkyOne UAVs encounter during real flights. As opposed to a single UAV test flight, the MAST can shake SkyOne for hours or even days at a time (simulating a long, non-stop flight). This allows SkyX to gather data on the strengths, potential weaknesses and maximum durability of the UAV in a much shorter timeframe than multiple real-time flights would permit.
Sensors measure responses from multiple points on the UAV. Engineers can instantly monitor specific details on how SkyOne reacts to movement in various directional/force modes, verify its stability and demonstrate its structural integrity.
Climatic Wind Tunnel testing process at ACE
ACE’s Climatic Wind Tunnel is one of the world’s most advanced wind tunnels, capable of simulating the most extreme weather conditions by varying the temperature (minus 40 to plus 60 Celsius), wind (in excess of 260 km/h) humidity (5 to 95 per cent), precipitation (rain, snow, ice) and solar intensity.
At ACE, SkyX was able to visualize and gather data on how air currents move over the wing and fuselage of the UAV. ACE engineers designed a force-balance within an adjustable rotational pivot located on an airfoil (wing-shaped) post. This tool allowed SkyX to calculate precise drag and lift measurements, and understand how air moves over SkyOne at different flight angles.